Associations:
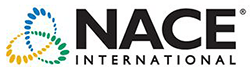
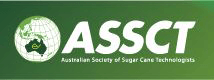
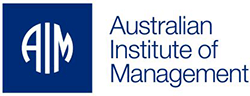
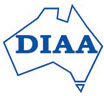
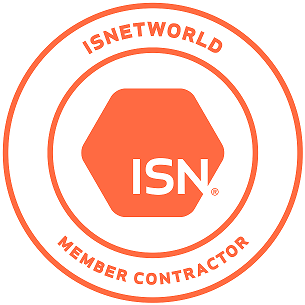
Employee and customer safety is our number one goal in any steam plant chemical cleaning exercise & we believe that all injuries are preventable. We continually train all Supervisors & Technicians to ensure a safe work environment on each and every job. Another major objective of all steam boiler programs is to minimise energy consumption by keeping boiler fuel and water sides free from insulating deposits.
As little as 1 mm of waterside deposit can result in an energy loss of 5 - 6% which is substantial.
Any deposit water side is too much so a boiler developing insulating deposits for whatever reason needs to be returned to clean condition quickly.
The process for CORE is:
- To collect a deposit sample for analysis to ensure an effective cleaning process
- To attend site risk management assessments
- To prepare all procedures/Work Method Statements/Environmental JSA
Once this is completed chemicals and equipment are mobilised to site where the clean & passivation process begins. This involves however is not limited to:
- the use of specialised pumps/tanks/hoses
- testing the cleaning solution hourly for acid strength/iron/temp./inhibitor
- collecting and correct disposal of cleaning solution
- thorough washing of boiler internals
- passivating boiler internals to ensure equipment is returned to service not only deposit free but with metal surfaces passive
Payback on deposit removal from steam boilers is short term, usually months.
Contact us today to find out more!